Electric guitars have been at the forefront of modern music for decades, captivating audiences with their versatile sounds and iconic designs. “What are electric guitars made of?” is a question that often intrigues both aspiring musicians and seasoned players alike.
The materials used in electric guitar construction play a crucial role in shaping the instrument’s tone, playability, and overall character. From traditional woods like alder and mahogany to modern synthetic materials such as carbon fiber, electric guitars showcase a diverse range of components that contribute to their unique qualities.
Knowing about these materials not only provides insight into the craftsmanship behind these instruments but also helps players make informed decisions when choosing or customizing their guitars. As technology advances, the world of electric guitar materials continues to evolve, offering new possibilities for sound and design.
Key Takeaways:
- Electric guitars utilize a diverse range of woods for bodies and necks, including alder, ash, mahogany, and maple, each contributing unique tonal characteristics and playing experiences.
- Synthetic materials like carbon fiber and graphite are increasingly used in electric guitar construction, offering enhanced stability, lightweight properties, & resistance to environmental changes.
- The choice of materials significantly impacts an electric guitar’s weight, balance, and playability, with denser woods like mahogany resulting in heavier instruments compared to lighter options like basswood.
- Fretboard materials such as rosewood, maple, and ebony affect both the feel and tonal qualities of electric guitars, with each wood type offering distinct playing characteristics & aesthetic.
- Innovative manufacturing techniques, including 3D printing, are enabling new possibilities in electric guitar design, allowing for complex body shapes and customized components made from both traditional and modern materials.
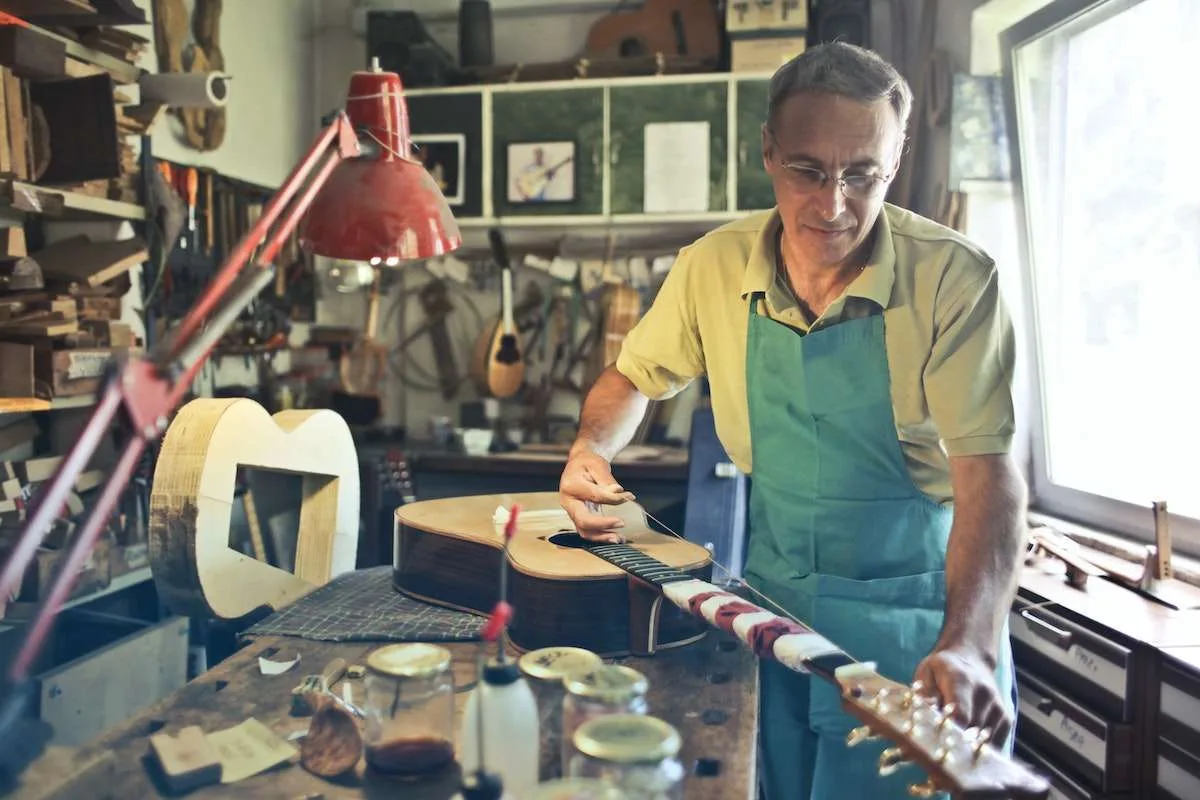
Introduction to Guitar Materials
The materials used in guitar construction have played a crucial role in shaping the instrument’s evolution, sound, and playability. From traditional woods to modern synthetics, each material brings unique properties that influence the guitar’s tone, durability, and aesthetic appeal.
Brief history of guitar materials
Guitars have a rich history dating back centuries, with materials evolving alongside technological advancements and changing musical needs. Early guitars were primarily constructed from wood, with luthiers favoring materials like spruce, cedar, and various hardwoods for their tonal properties and availability.
In the early 20th century, with the advent of electric guitars, manufacturers began experimenting with new materials. The 1950s saw the introduction of solid-body electric guitars, utilizing woods like ash and alder. As the century progressed, synthetic materials like plastics and metals were incorporated into various guitar components.
The late 20th and early 21st centuries have witnessed a surge in material innovation, with the introduction of carbon fiber, graphite, and other high-tech materials in guitar construction. These advancements have allowed for greater experimentation in design and sound, while also addressing concerns about sustainability and endangered wood species.
Importance of material choice in guitar construction
The choice of materials in guitar construction is paramount for several reasons:
- Tonal qualities: Different materials vibrate and resonate in unique ways, directly impacting the guitar’s sound. For instance, mahogany tends to produce a warm, rich tone, while maple offers a brighter, more articulate sound.
- Playability: The weight and feel of the guitar are greatly influenced by its materials. Lighter woods or synthetic materials can make a guitar more comfortable for extended play, while denser materials might offer better sustain.
- Durability: Some materials are more resistant to environmental factors like humidity and temperature changes, affecting the guitar’s longevity and stability.
- Aesthetics: The visual appeal of a guitar often stems from its materials, with exotic woods or unique finishes attracting players and collectors alike.
- Sustainability: As awareness of environmental issues grows, the choice of sustainable or alternative materials becomes increasingly important in guitar manufacturing.
- Cost: Material selection significantly impacts the final cost of the instrument, with rare woods or high-tech materials often commanding premium prices.
Understanding the properties and implications of different guitar materials allows manufacturers to create instruments tailored to specific needs and preferences, while also enabling players to make informed decisions when choosing their ideal guitar.
Components of an Electric Guitar
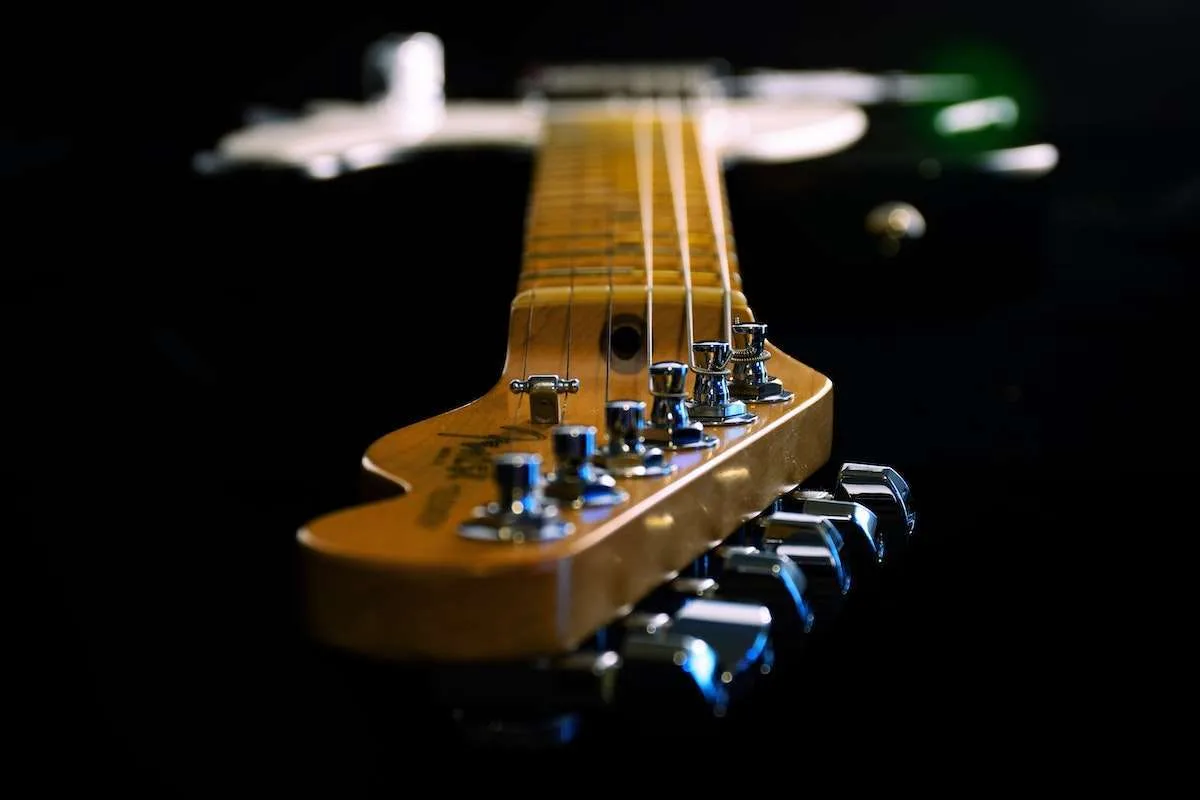
An electric guitar is made up of several components that work together to produce the sound that you hear. These components can be divided into different sections such as the body, neck, strings, pickups, bridge, frets, tuners, and knobs. In this section, we will take a closer look at each of these components and their role in creating the sound of an electric guitar.
Body
The body of an electric guitar is typically made of wood, although other materials such as carbon fiber and aluminum are sometimes used. The shape and size of the body can vary depending on the model of the guitar, but it generally has a hollow or semi-hollow design. The body of the guitar is where the pickups, bridge, and knobs are mounted.
Neck
The neck of an electric guitar is usually made of wood and is attached to the body of the guitar. The neck is where the frets and tuning machines are located. The neck can be either bolted or glued to the body of the guitar, depending on the model.
Strings
The strings of an electric guitar are made of steel or nickel and are responsible for producing the sound of the guitar. The strings are stretched across the body and neck of the guitar and are held in place by the bridge and nut.
Pickups
The pickups of an electric guitar are responsible for converting the vibrations of the strings into an electrical signal that can be amplified. There are two main types of pickups: single-coil and humbucker. Single-coil pickups produce a bright and clear sound, while humbucker pickups produce a warmer and fuller sound.
Bridge
The bridge of an electric guitar is where the strings are anchored to the body of the guitar. The bridge can be either fixed or floating, depending on the model of the guitar. The bridge also affects the intonation and action of the guitar.
Frets
The frets of an electric guitar are the metal strips that are embedded into the neck of the guitar. The frets are used to change the pitch of the strings when they are pressed down against them. The number of frets on an electric guitar can vary depending on the model.
Tuners
The tuners of an electric guitar are responsible for adjusting the pitch of the strings. The tuners are located on the headstock of the guitar and can be either locking or non-locking. Locking tuners help to keep the guitar in tune for longer periods of time.
Knobs
The knobs of an electric guitar are used to adjust the volume and tone of the guitar. The knobs are located on the body of the guitar and can be either push-pull or standard. Push-pull knobs allow for additional tonal options.
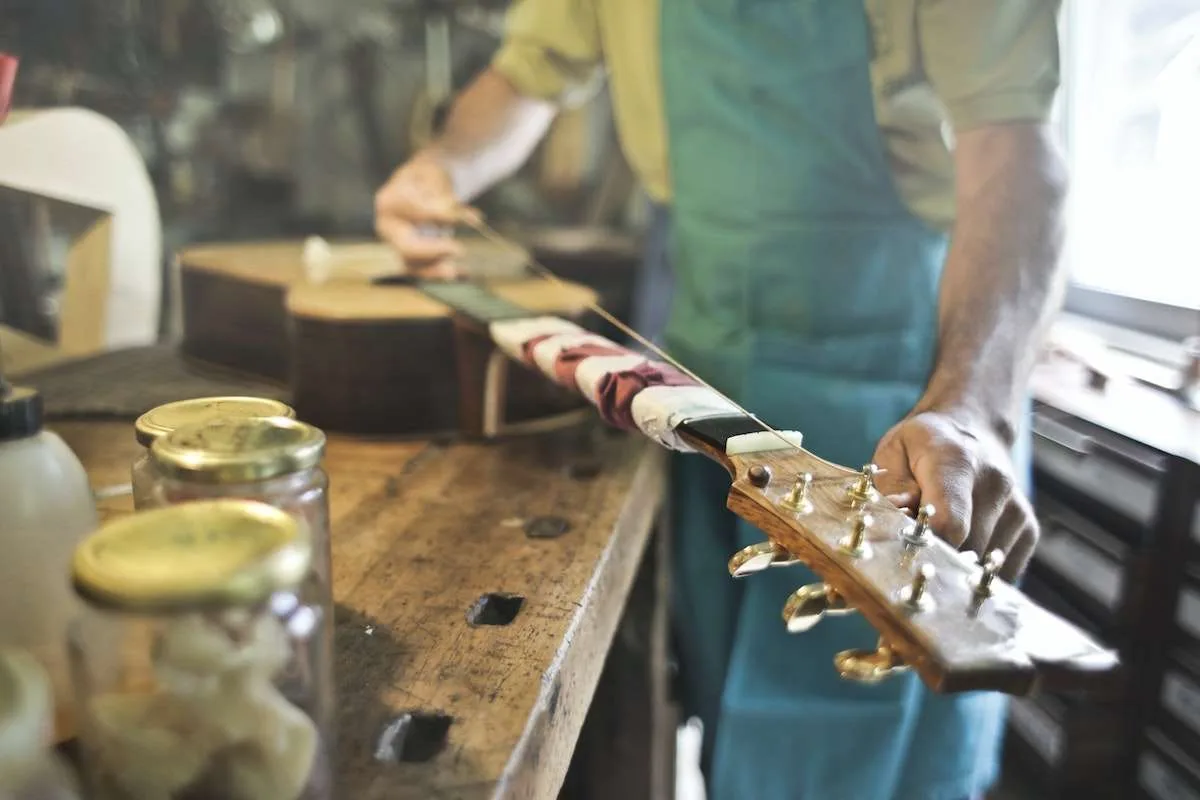
Electric Guitar Materials
Electric guitars offer a diverse range of material options, allowing for greater experimentation in tone, weight, and design compared to their acoustic counterparts. The choice of materials significantly impacts the instrument’s sound, playability, and aesthetic appeal.
Body Woods:
- Alder: Balanced tone with slight emphasis on upper midrange, popular in many Fender models.
- Ash: Bright, resonant tone with strong sustain, often used in Telecasters and other Fender guitars.
- Mahogany: Warm, rich tone with strong bass response, common in Gibson Les Pauls and SGs.
- Basswood: Lightweight with a balanced tone, popular in budget and mid-range guitars.
- Maple: Bright, punchy tone with excellent sustain, often used as a top wood or in neck-through designs.
Neck Woods:
- Maple: Provides stability and a bright tone, commonly used in Fender-style guitars.
- Mahogany: Offers warmth and resonance, frequently used in Gibson-style guitars.
- Rosewood: Often used for fretboards, providing a smooth feel and warm tone.
Fretboard Woods:
- Rosewood: Warm tone and smooth feel, traditionally popular but facing sustainability issues.
- Maple: Bright tone and distinct appearance, common on Fender-style guitars.
- Ebony: Smooth, dense wood offering clarity and brightness.
- Pau Ferro: Sustainable alternative to rosewood, offering similar tonal qualities.
Alternative & Modern Materials in Electric Guitars
Synthetic materials (carbon fiber, graphite, etc.)
Carbon fiber is increasingly used in electric guitar construction for its strength, light weight, and resistance to environmental changes. It’s found in necks, bodies, and even full guitars, offering clear tone and exceptional stability. Companies like Rainsong and Blackbird have pioneered all-carbon fiber electric guitars, while others like Parker Guitars have incorporated carbon fiber elements into more traditional designs.
Graphite, often used in necks and reinforcement rods, provides excellent sustain and consistent performance across climates. Vigier Guitars, for example, uses a proprietary graphite neck in many of their models. Richlite, a paper-based composite, serves as a sustainable alternative to ebony for fretboards and is used by major manufacturers like Gibson in some of their electric guitar models.
Composite materials
Wood-plastic composites blend wood fibers with thermoplastic, offering improved stability and moldability for electric guitar bodies. These materials can mimic the tonal properties of traditional woods while providing enhanced durability and consistency.
Flaxwood, made from natural fiber composites, provides tonal consistency and sustainability. This material is used to create entire electric guitar bodies and necks, offering a unique alternative to traditional wood construction.
Some innovative electric guitar designs incorporate aluminum or other metal elements in their construction. For instance, Travis Bean and Kramer guitars from the 1970s used aluminum necks for increased sustain and stability.
3D-printed guitar components
3D printing enables complex body designs and customization options previously impossible in electric guitar manufacturing. Companies like Olaf Diegel’s ODD Guitars create intricate, one-of-a-kind electric guitar bodies using 3D printing technology.
Some manufacturers are exploring 3D-printed necks with integrated electronics and internal reinforcement structures for electric guitars. This technology allows for precise control over weight distribution and tonal characteristics.
3D-printed hardware, including bridges and pickups, allows for rapid prototyping and customization in electric guitar design. This technology enables manufacturers to quickly test and refine new component designs.
These innovations address sustainability, consistency, and customization in electric guitar manufacturing, offering players new options in tone, playability, and design alongside traditional materials. As technology advances, we can expect to see even more integration of these modern materials and manufacturing techniques in electric guitar production.
How Materials Affect Electric Guitar Properties
Tone & Sound Quality
While the impact of materials on electric guitar tone is a subject of ongoing debate, many guitarists and luthiers believe that different woods contribute to tonal characteristics:
Material | Perceived Tonal Characteristics in Electric Guitars |
---|---|
Alder | Often associated with balanced tone, slight upper midrange emphasis |
Ash | Known for bright, resonant tone with strong sustain |
Mahogany | Typically produces warm, rich tone with strong bass response |
Maple | Commonly described as bright and punchy with excellent sustain |
It’s important to note that in electric guitars, pickups and electronics play a significant role in shaping the final tone, often overshadowing subtle differences in wood types. The wood’s influence on tone is generally more subtle in electric guitars compared to acoustic instruments.
Weight & Playability
Material choices significantly affect an electric guitar’s physical properties:
- Body weight: Denser woods like mahogany typically result in heavier guitars, while lighter woods like basswood or alder produce lighter instruments. This affects both playability and sustain.
- Neck material: The choice of neck wood influences the guitar’s balance and overall weight distribution. Maple necks, for example, are often stiffer and brighter-sounding than mahogany necks.
- Fretboard: Different materials affect the feel under the fingers, potentially influencing playability. Rosewood, maple, and ebony are common choices, each with distinct characteristics.
- Balance: The combination of body and neck materials affects how the guitar feels when played standing up, which is crucial for live performances.
Durability & Maintenance
Different materials used in electric guitars have varying properties that affect longevity and care requirements:
Aspect | Consideration for Electric Guitars |
---|---|
Environmental response | Some woods may be more reactive to humidity and temperature changes, affecting neck stability and fret integrity |
Finish types | Different finishes offer varying levels of protection and may affect maintenance needs. Nitrocellulose vs. polyurethane finishes, for example, age differently |
Fretboard wear | Harder woods like ebony generally show less wear over time compared to softer woods like rosewood |
Hardware quality | Material choice in hardware (e.g., nickel vs. stainless steel frets) can affect long-term performance and maintenance needs |
The selection of materials can influence how an electric guitar ages and the level of maintenance required. However, proper care and storage are crucial for any electric guitar, regardless of its materials.
While material choices affect these properties, other factors such as construction techniques, pickup types, electronics, and individual manufacturing variations also play significant roles in an electric guitar’s overall performance and feel. The interplay between these elements creates the unique character of each instrument.
Environmental Considerations in Electric Guitar Materials
Sustainable wood sourcing
Many electric guitar manufacturers are adopting responsible sourcing practices, partnering with organizations like the Forest Stewardry Council (FSC) to ensure their wood comes from sustainably managed forests. This approach helps preserve ecosystems while maintaining a supply of quality tonewoods for future electric instruments. Companies like Fender and Gibson have implemented programs to source woods like ash and maple from certified sustainable forests.
Alternatives to endangered wood species
As traditional tonewoods become scarcer, electric guitar manufacturers are exploring alternatives:
- Richlite: A paper-based composite used as an alternative to ebony for electric guitar fretboards. It’s been adopted by major manufacturers like Gibson for some of their electric guitar models.
- Roasted maple: Heat-treated maple that offers improved stability and a vintage appearance, increasingly used in electric guitar necks and fretboards.
- Reclaimed wood: Repurposed from old buildings or furniture, reducing demand for new timber. Some boutique electric guitar makers specialize in using reclaimed wood for bodies and necks.
- Synthetic materials: Carbon fiber and other high-tech materials are being used in electric guitar construction, offering durability and consistency while reducing reliance on rare woods.
Eco-friendly electric guitar manufacturing practices
Electric guitar makers are implementing various eco-friendly practices:
- Water-based finishes: Reducing VOC emissions compared to traditional lacquers used on electric guitar bodies and necks.
- Energy-efficient production: Using renewable energy sources and optimizing manufacturing processes in electric guitar factories.
- Waste reduction: Implementing recycling programs for wood scraps and minimizing material waste in the production of electric guitar bodies and necks.
- Local sourcing: Reducing transportation emissions by using locally available materials when possible for electric guitar components.
- Improved durability: Designing electric guitars with better resistance to environmental changes, reducing the need for replacements and repairs.
These practices aim to reduce the environmental impact of electric guitar production while maintaining instrument quality and meeting player expectations. As awareness grows, more electric guitar manufacturers are prioritizing sustainability in their production processes, from material sourcing to packaging and distribution.